
Advantages and Disadvantages of Induction Heating for Welding
Induction heating for welding has its own (advantages and disadvantages!) that should be considered before investing in this type of technology. One advantage is the speed at which it is able to heat metal; induction can do this faster than traditional methods, making welds quicker and more efficient. Additionally, it uses less energy than other methods, saving money on electricity bills. However, there are a few drawbacks too. Firstly, induction heating requires specialised equipment which can be expensive to buy or rent. Furthermore, it isn't suitable for all types of metals; some may not respond well to the process or require additional safety measures due to high temperatures created during welding. Lastly, welders must have knowledge of how to use induction welders correctly as they require skillful operation for best results. In conclusion, induction heating provides many advantages but also comes with some downsides to consider before investing in it. Although it is speedy and cost-effective compared to other welding methods, extra safety measures and specialist equipment must be accounted for when using this technology. Nevertheless, with appropriate training and attention given to safety protocols, induction welding can be a powerful tool!
read more
What is the Secret to Faster, Stronger, and More Durable Welds?
The secret to faster, stronger and more durable welds is something every welder wants to know! It's not an easy task, but with the right technique and materials, anyone can achieve great results. Firstly, it's important to ensure that both surfaces are properly prepared. This means making sure that they're free from rust or other debris which could weaken the bond. Additionally, you want to make sure your work area is well ventilated and free from dangerous fumes. Another key factor in successful welding. Next up, select a compatible material for your job - steel works best for most applications. Then use a high-quality electrode (that's what creates the heat needed for welding) and set it at the correct voltage for your job. Finally, don't forget to wear proper safety equipment; like goggles and gloves - this will ensure you remain safe during the process! Once everything is ready, it's time to get welding! For best results, maintain a constant speed while moving the torch slowly across the surfaces. Try not to linger in one spot too long as this can cause distortions in the metal. Also be sure not to overheat any of
read more
What Are the Benefits of Investing in Induction Heat Treatment Technology?
Investing in Induction Heat Treatment Technology has a multitude of advantages! Not only does it reduce manufacturing costs, but it also increases efficiency and quality. (Plus, the process is environmentally friendly!) It's no wonder why so many companies are turning to this technology for their production needs. First of all, induction heat treatment can decrease labor costs significantly. The process requires minimal manpower input and allows companies to save on expensive personnel expenses. Furthermore, since the whole system is automated, there's less chance of human error - resulting in a more consistent product output. All these factors contribute to a decrease in overall cost. Moreover, induction heat treatment streamlines the entire production process. Since it's fully computer-controlled, there's less opportunity for delays or mistakes during production which leads to fewer missed deadlines and fewer scrapped parts. Plus, with its precise temperature control capability, products can be produced with greater accuracy and repeatability - thus increasing quality assurance as well as customer satisfaction! Furthermore, this technology is eco-friendly too! Unlike other processes such as gas or flame heating that produce harmful emissions into the atmosphere; induction heat treatment doesn't release any hazardous
read more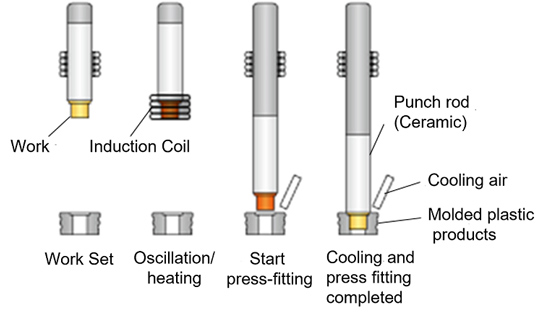
Intro to Induction Welding and Induction Heating
Prepping pipes and other surfaces for welding can be a real challenge since metal surfaces often need to be hot before you begin. If the metal isn’t hot enough before you start welding, it will affect the cooling rate. If a weld cools too quickly, the metal could go into shock and cause fabrication hydrogen cracking. There are many metal preheating methods. Some of these include: furnace heating, torching, electrical strip heaters, induction heating, and radiation heating, and welding preheat blankets. Hydrogen-assisted cracking is a major challenge in underwater wet welding of high-strength steels with a carbon equivalent larger than 0. 4 wt%. In dry welding processes, post-weld heat treatment can reduce the hardness in the heat-affected zone while simultaneously lowering the diffusible hydrogen concentration in the weldment. However, common heat treatments known from atmospheric welding under dry conditions are non-applicable in the wet environment. Induction heating could make a difference since the heat is generated directly in the workpiece. In the present study, the thermal input by using a commercial induction heating system under water was characterized first. Then, the effect of an additional induction heating was examined with respect to the resulting microstructure of weldments on structural
read more
Miller Induction Heating - How it Works
Pdf 2 miller induction technology boosts productivity, reduces hydrogen cracking in pipeline applications induction technology provides a fast, safe and consistent heating method for pre- and post-weld heat treatment, to help minimize the risk of weld failure due to hydrogen-induced cracking in high-strength steels. The proheat 35 is an air cooled induction system for preheat applications up to a maximum preheat temperature 204°c (400°f) the proheat 35 liquid-cooled system can be operated in manual programming mode where a power output is applied to a part for a specified time or in the temperature based programming mode where the part temperature is used to control power output. Pre-heating of a valve body to 400°f before welding on a repair. Water-cooled induction coils (miller patented) are flexible and easy to apply to a variety of geometries. Here a “pancake” style coil has been wrapped around a repair area. Typical heat time for this application is 10-15 minutes for both the inside and outside of the body to be at temperature. Note also that this coil is protected with pre-heat covers to protect the coil from hot weld slag and abrasive wheels. Because the heat is in the valve and not the coil, rope,
read more