Intro to Induction Welding and Induction Heating
by Admin
Posted on 21-06-2023 12:37 PM
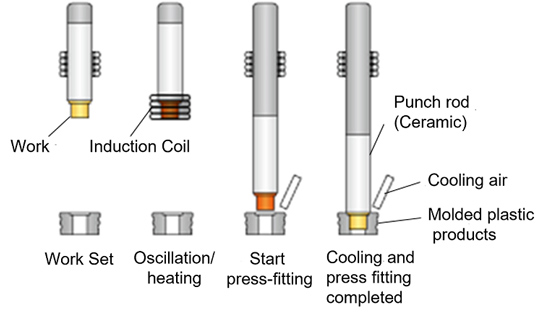
Prepping pipes and other surfaces for welding can be a real challenge since metal surfaces often need to be hot before you begin. If the metal isn’t hot enough before you start welding, it will affect the cooling rate. If a weld cools too quickly, the metal could go into shock and cause fabrication hydrogen cracking. There are many metal preheating methods. Some of these include: furnace heating, torching, electrical strip heaters, induction heating, and radiation heating, and welding preheat blankets.
Hydrogen-assisted cracking is a major challenge in underwater wet welding of high-strength steels with a carbon equivalent larger than 0. 4 wt%. In dry welding processes, post-weld heat treatment can reduce the hardness in the heat-affected zone while simultaneously lowering the diffusible hydrogen concentration in the weldment. However, common heat treatments known from atmospheric welding under dry conditions are non-applicable in the wet environment. Induction heating could make a difference since the heat is generated directly in the workpiece. In the present study, the thermal input by using a commercial induction heating system under water was characterized first. Then, the effect of an additional induction heating was examined with respect to the resulting microstructure of weldments on structural steels with different strength and composition.
An operator replaces a bearing that has been heated with an enrx mobile minac system enrx systems have been used for hot tap welding on the bed of the north sea: photo: technip norge as. Specialist coils being tested for the tampen subsea hot tapping procjet. Photo: technip norge as an medium-frequency enrx sinac pre-heats seamless offshore pipe prior to coating. No dust, no fumes, no noise. An enrx heater gets to grips with 170 mm anode stubs. Induction heating is increasingly used to remove the giant nuts and bolts in power stations’ turbines. Enrx designs and builds specialised systems for steel strip and wire and cable pre-heating.
Fire, Spark & Fume Protection
Deke home makes beautiful and great blankets with classic and higher-grade materials.
The deke home induction heating blanket for welding is made of flame retardant fiberglass and has a working temperature of 1, 000 degrees fahrenheit, this blanket is essential for welding safety. Protect your furniture, flooring, wood railings, and yourself from sparks, embers, molten metal, and heat that comes from welders, grills, smokers, and more. Also, this is built to last and it stands up for the long-term. Above all, the deke home induction heating blanket for welding provides thermal protection from sparks and spatter. Almost all buyers agree that the blanket is constantly shedding fiberglass and also fits well and has so far prevented burns.
What is induction heating?
Time to temperature is dramatically faster than flame or resistance heating -- reducing cycle time. Setup and tear down times are quick and unlike flame or resistance, induction allows continuous heating and fabrication. Induction heating lowers operational costs because reaching target temperatures is dramatically faster, resulting in reduced consumable costs and labor expenses. In addition, it eliminates the expense of fuel gases, fire watch personnel*, and heating subcontractors. Provides exceptional joint temperature uniformity. Induction eliminates the inconsistencies and quality issues associated with flame or resistance heating. Welders are not exposed to open flame, explosive gases, and hot elements associated with flame and resistance heating.
1. Wide and even heating zone the width is sufficient to cover the uniform heating zone of the post-weld heat treatment specified by asme. 2. High-precision temperature control frequency conversion control power supply can realize precise heating/heat preservation/cooling steps. 3. High security unlike annealing of resistance heating elements, non-heated induction coils ensure a high degree of safety. 4. Easy installation one-button operation coil (the built-in coil piece is placed around the pipe), which is easier to fix and disassemble than the induction coil wound on the pipe.
Induction heating provides a consistent, efficient, and focused solution for thermal processing of parts and components. Processing cycle times and energy usage can be significantly reduced when compared to other processes. Induction heating is also ideal for providing a stable and repeatable process to produce a high volume of parts with consistent quality. As a system integrator, taylor-winfield technologies offers a wide range of standard and custom induction heating solutions. From a standalone power supply to a fully automated, turn-key system, taylor-winfield technologies is your go-to resource for a variety of thermal solutions.
Induction heating is used to manufacture end items as diverse as bulldozers, spacecraft, faucets and sealing plastic lids on pharmaceutical bottles. The fundamental design of an induction heating device uses a coil of wire and an ac current to induce a changing magnetic field in the item to be heated—the work piece. The coil can measure only a few centimeters in diameter, or any other dimension suited to the job at hand. The work piece is placed inside the magnetic field generated by the coil, but not in contact with it, then heated to the desired level by the eddy currents.
Because induction heating is accomplished using a magnetic field, the work piece (or load) can be physically isolated from the induction coil by refractory or some other non-conducting medium. The magnetic field will pass through this material to induce a voltage in the load contained within. This means that the load or work piece can be heated under vacuum or in a carefully controlled atmosphere. This enables processing of reactive metals (ti, al), specialty alloys, silicon, graphite, and other sensitive conductive materials.
Mis's induction heating system can save hours and even days during scheduled turbine outages. Our induction heating technology reduces the average time from 45 minutes per bolt to 5 minutes per bolt and the induction coils are cool to the touch, creating a safer work environment. Our complete line of on-site services and equipment enable you to reduce downtime and make your next outage safe, quick and cost-efficient. Mis's turbine bolt heating system utilizes variable-frequency inductive equipment and processes to thermally elongate turbine bolts in the fraction of the time normally required for the operation. These specially designed inductors make it possible for all heated bolting to be removed or tightened within one shift or less.